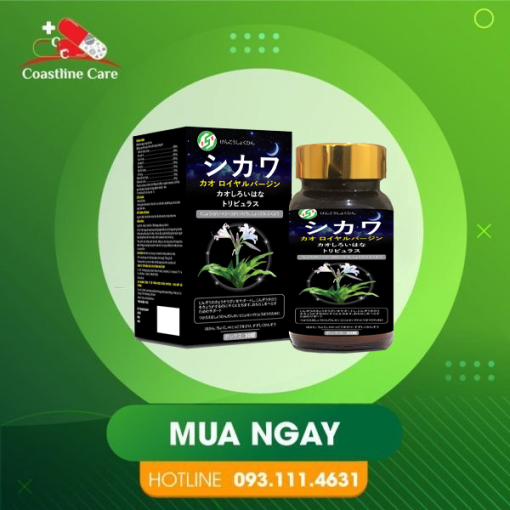
Units - What overarching processes are in position, And the way can they be improved or altered to better serve a buyer?
These are named following Japanese engineering professor Kaoru Ishikawa during the 1960s, who assisted use them to producing procedures.
Updated: February 3, 2025 by Matthew Barsalou Root induce analysis (RCA) is actually a strategy for pinpointing the underlying source of a process or products failure. Therefore, then the appropriate solution is often determined. RCA can development more quickly and properly by pairing an Ishikawa diagram.
If your hypothesis is not really supported, then the next one particular in the prioritized monitoring record must be chosen and evaluated.
Recycling the technique, producing sub-hypotheses or sequential hypotheses to refine the chances that stay, and so on
This Site is utilizing a safety provider to shield alone from on the net assaults. The action you just done induced the safety Resolution. There are various steps that would result in this block including distributing a particular term or phrase, a SQL command or malformed facts.
The Ishikawa Diagram remains a essential tool in excellent Manage, and good quality circles go on being a beneficial nha thuoc tay exercise in many organizations.
It can help you target your endeavours on the almost certainly motives. Here are a few distinctive high quality administration tools You can utilize to kind and prioritize probable results in; Some involve:
Kaoru Ishikawa’s contributions have experienced a lasting impact on good quality administration practices throughout the world. His emphasis on involving all staff members in the quality course of action has triggered much more collaborative and successful challenge-resolving methods.
Each trigger or basis Shikawa for imperfection can be a supply of variation. Results in are generally grouped into key groups to identify and classify these sources of variation.
Assess the Diagram: Evaluate the diagram to determine associations and prioritize will cause nha thuoc tay for additional investigation. It is possible to prioritize working with genuine information, multivoting, nominal group methods, or gaining consensus from your crew.
Under is undoubtedly an illustration of a fishbone diagram for the production firm. In this circumstance, the business employs the 6Ms to higher realize the results in of the trouble, and that is that a Component of the product is in the wrong dimension.
This kind of tracking listing will also be utilized to communicate the staff’s progress to management and consumers. New insights may very well be gained since the investigation progresses. Such as, somebody checking the size of an element could have noticed problems. This damage could then be entered into an up-to-date Ishikawa diagram and after that transferred to your tracking record.
Ishikawa diagrams were being popularized within the nineteen sixties by Kaoru Ishikawa,[four] who pioneered quality management processes during the Kawasaki shipyards, and in the procedure became one of several founding fathers of modern administration.